Silicone is a top choice for applications exposed to environmental factors that can degrade other materials. Known for its exceptional temperature resistance, silicone rubber performs reliably in both high and low extremes. It also outperforms conventional rubbers in tensile strength, elongation, tear resistance, and compression set in extreme conditions.
Beyond temperature resistance, silicone rubber offers additional benefits, including excellent electrical insulation, water repellence, and compression set resistance. These properties make it a highly versatile material, ideal for creating durable rubber products that thrive in demanding environments.
At Uma Rubber, we specialize in providing businesses with custom silicone gaskets, tubing, and other parts designed to meet specific application requirements, ensuring long-lasting performance even in challenging conditions.
What is Silicone Rubber Made Of?
Silicone, a synthetic rubber, is not naturally occurring. Its origins are debated—some attribute its discovery to Swedish chemist Jöns Jacob Berzelius in the early 1800s, while others credit English chemist Frederick S. Kipping in 1840. Regardless of its exact origins, silicone rubber gained widespread popularity in the early 20th century, becoming a vital material across numerous industries.
The production of silicone rubber begins with isolating silicon, a chemical element derived from silica. Quartz sand is subjected to extreme heat to produce pure silicon, which is then cooled and ground into a fine powder. This silicon powder is a key material used in applications ranging from semiconductors to fire bricks.
To create silicone elastomers, the silicon powder is heated with methyl chloride and polymerized with oxygen and other elements to form polysiloxane. This base material can then be mixed with pigments and additives to achieve specific properties and characteristics. The final silicone rubber is processed through extrusion, molding, or other manufacturing techniques to produce parts ready for diverse applications.
Silicone Rubber Properties
- Common Name: Silicone
- ASTM D-2000 Classification: FC, FE, GE
- Chemical Definition: Polysiloxane
- Temperature Range
- Low Temperature Usage: -60° to -150° F | -50°C to -100°C
- High Temperature Usage: Up to 480° F | Up to 250°C
- Tensile Strength
- Tensile Range: 200-1500 P.S.I.
- Elongation: 700% Maximum
- Durometer (Hardness) – Range: 30-90 Shore A
- Resistances
- Abrasion Resistance: Fair to Poor
- Tear Resistance: Poor
- Solvent Resistance: Poor
- Oil Resistance: Fair to Poor
- Aging Weather – Sunlight: Excellent
- General Characteristics
- Adhesion to Metals: Good
- Compression Set: Good
- Resilience/Rebound: Good
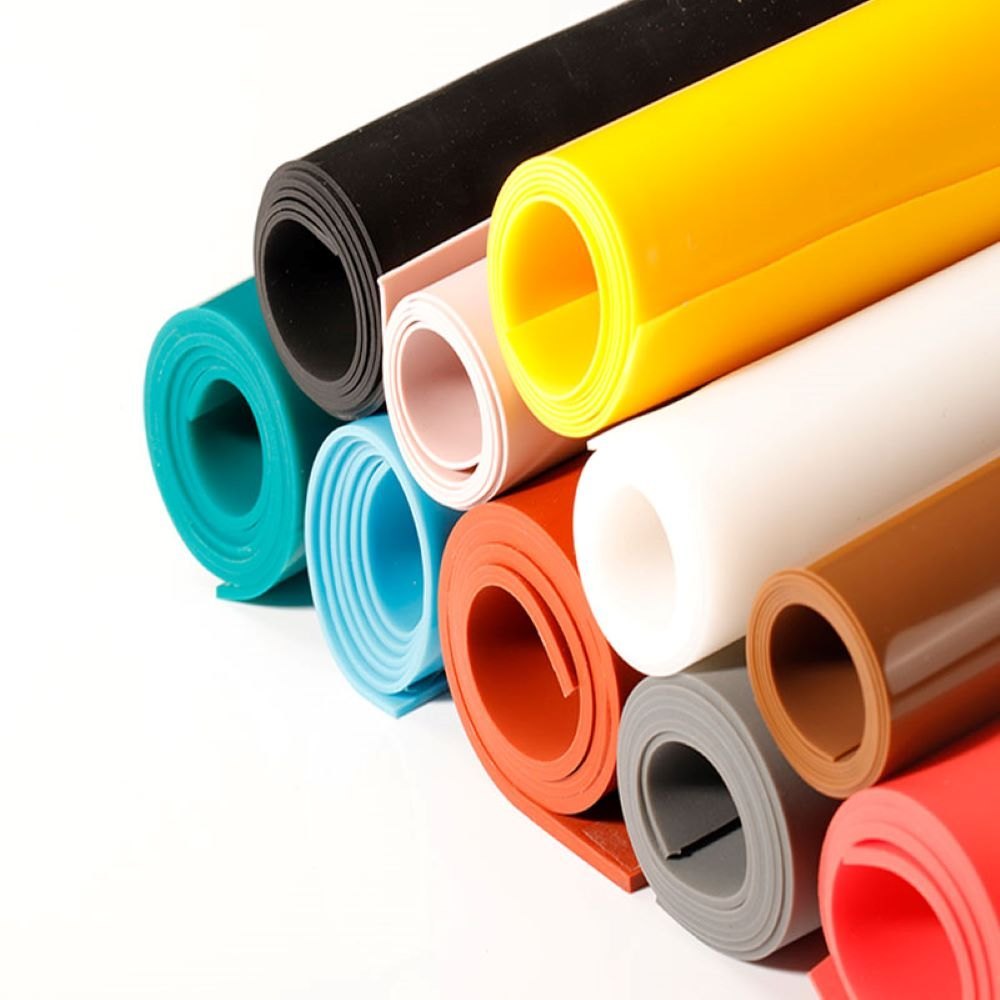
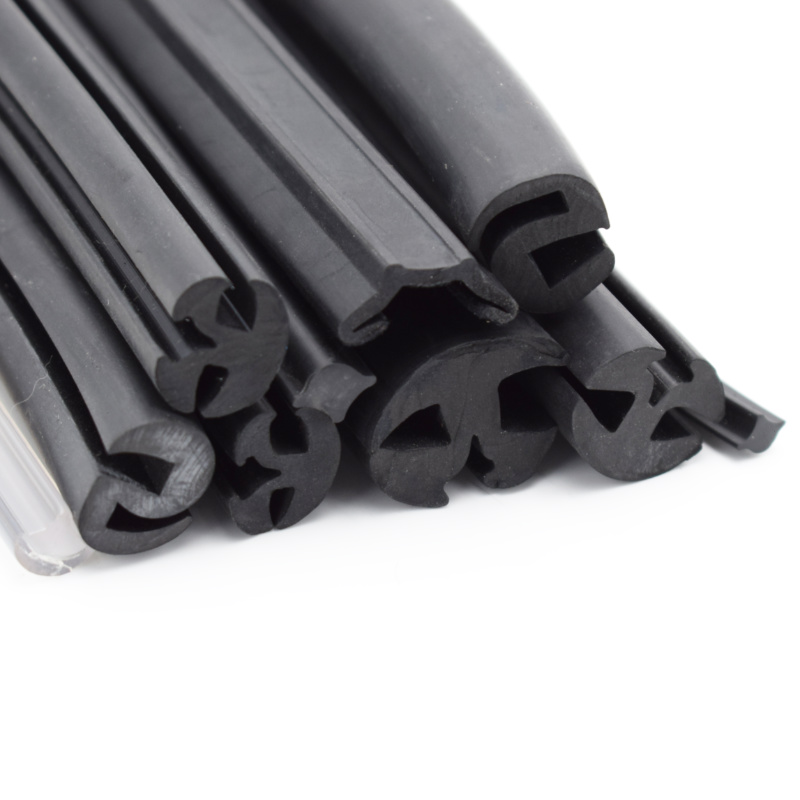
Silicone Rubber Applications
Automotive
- Sound and vibration dampening in automotive drive shafts
- Shaft sealing rings
- O-rings
- Window and door seals
HVAC
- Square, kink-free tubing
- High-temperature gaskets
- O-rings
Electrical
- Wire and cable jacketing
- Electrical safety stinger covers
- Conductive profiled silicone seals
Home appliances
- Rubber tubing
- Appliance seals
- O-rings
- Sound and vibration dampeners
Interested in Silicone Rubber and its Products?
Call +91 70696 80580 or complete our online form to request a quote.
Not sure which material you need for your custom rubber product? You are just a click away Contact Us.